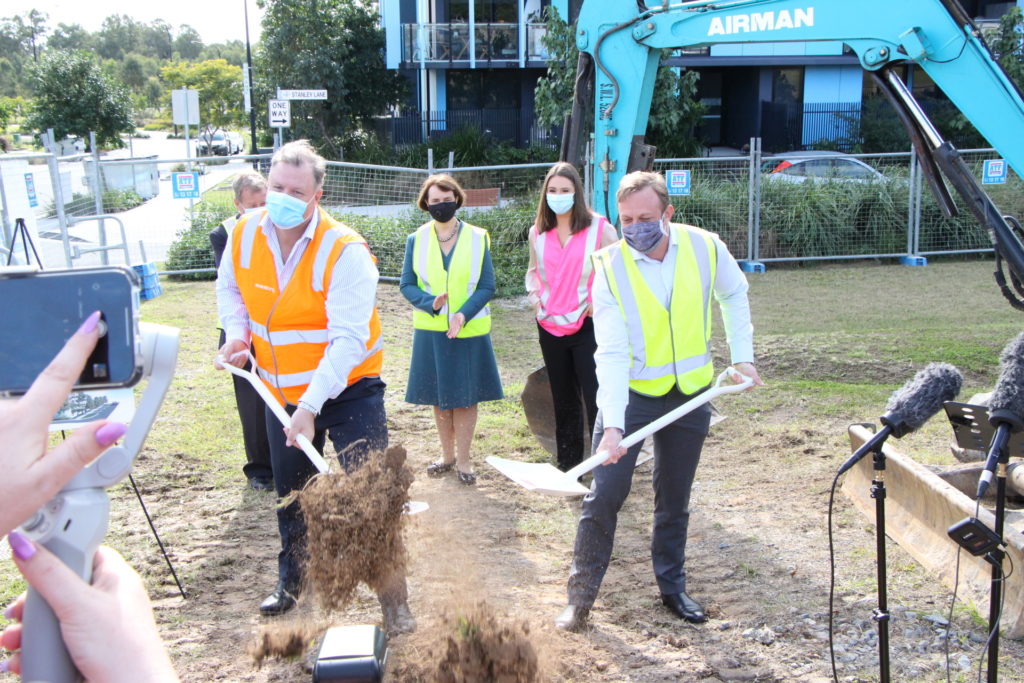
Up to 30 Griffith University researchers and PhD students will develop innovative programs and early interventions for young children, including those with additional needs, through co-locating with a new early learning centre and paediatric clinicians from Gold Coast Health in the Gold Coast Health and Knowledge Precinct.
Deputy Premier and Minister for State Development Steven Miles was joined by Minister for the Environment, Great Barrier Reef, Science and Youth Affairs Meaghan Scanlon, Griffith University Vice Chancellor Professor Carolyn Evans, Gold Coast Hospital and Health Services Board Chair Ian Langdon, and representatives of developer Evans Long to turn the first sod on the new Proxima development, which will be focused on child health and development and is set for completion at the end of 2022.
The Deputy Premier and Minister Scanlon said founding tenant Sanctuary Early Learning Adventure would create a unique environment that will include support for children with special needs. Approximately 25 percent of the children who will use the inclusive centre are anticipated to have additional needs.
“This is an Australian-first, an early learning centre with in-house access to allied paediatric health and research professionals, and I’m so pleased they have chosen to establish within Lumina at the Gold Coast Health and Knowledge Precinct,” Mr Miles said.
Around 180 construction jobs will be created and when fully occupied, 900 health and teaching jobs will be based at Proxima, providing access to a huge range of services for families.”
“Children will have access to the expert care that they need within a familiar, fun and caring environment at their early learning centre, “Minister Scanlon said.
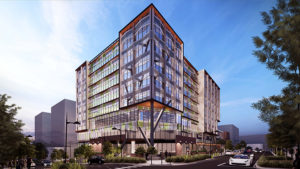
Professor Evans said co-location provided the perfect basis on which to establish a Centre of Excellence in Early Childhood Education.
“The Centre brings together interdisciplinary teams across Griffith’s Allied Health disciplines and Early Childhood Education to embed a model of research-integrated inclusive childcare education,” Professor Evans said.
“This will be a place in which every child can grow and learn together.”
Deputy Vice-Chancellor (Research) Professor Mario Pinto said a ‘living lab’ provides a rare and valuable opportunity for researchers and would build on the university’s existing strengths in education and autism research.
“This is all about collaboration, leveraging complementary skills, building on strong but flexible foundations as a springboard to a whole new level of research translation”.
“It is a perfect example of what our Research and Innovation Plan seeks to achieve with research impact, and what we are striving to create in the Precinct through integration.”
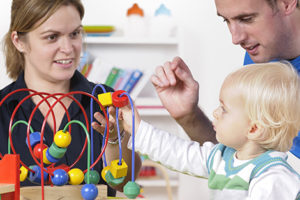
Associate Professor David Trembath, who will lead an allied health team of researchers from the university’s Menzies Health Research Institute Queensland, said the model would benefit both children with additional needs and the broader pre-school population.
“We will be looking at each child individually, rather than thinking of them through the lens of their diagnosis,“ Associate Professor Trembath said.
“It is all about identifying each child’s strengths, preferences, and interests and working with these. This is how all kids like to learn and doing so in an inclusive environment like this is good for all kids.
The close relationship with the diagnostic clinics at Gold Coast Health will also lead to children’s needs being identified in a timely way, so we can intervene at the earliest opportunity when it is most beneficial.”
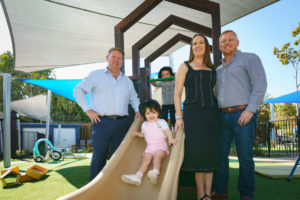
Sanctuary Early Learning Adventure Co-Founder, Damian Hall said the new state-of-the-art facility would cater for up to 400 children and they would have their own specialists embedded.
“Proxima will help relieve more of the pressure on parents also as it will eliminate most excess travel in transporting their children to and from medical appointments,” Mr Hall said.
Technology will be a focus for some educational supports, but equally researchers will learn practically through observing interactions between educators and children.
“For some children, technology will open new windows into how they think and learn, for children with minimal language it may open a new door to communication with their peers, parents, and teachers,” Assoc Prof Trembath said.
“We are working on offering training for Sanctuary’s staff and we will certainly be learning from them, and of course from the children themselves, so we can blend the art and science of early childhood development together.
The Director of the Menzies Health Research Institute Queensland, Professor Paul Scuffham played a key role in developing the concept.
“This exciting opportunity will allow for multi-year longitudinal studies as well as rolling evaluations in real-time that we will be able to quickly innovate into new programs,” Professor Scuffham said.
Griffith researchers will also be drawn from the Griffith Institute for Educational Research (GIER) and the University’s specialised Autism Centre of Excellence.